Disk brake
MIDIEL Group equips the manufactured lifting machines with a disc brake system of its own design with increased safety. The braking system of MIDIEL Group is a volumetric hydraulic drive consisting of a unified adjustable pump station, braking modules installed on pedestals, and automated electronic control equipment. The kinetic energy of the movement at the moment of braking is converted into thermal energy by the brake pads pressed against the brake disc of the drum by a set of disc springs. The reaction from the generated braking torque is taken up by the foundation. The degree of compression of the springs, and consequently the braking torque, is controlled by the pressure value of the hydraulic fluid supplied to the brake module working cylinders. Well-known normally closed disc brake modules BSFG 408A or BSFH 515 of SVENDBORG BRAKES A/S (Denmark) are used.
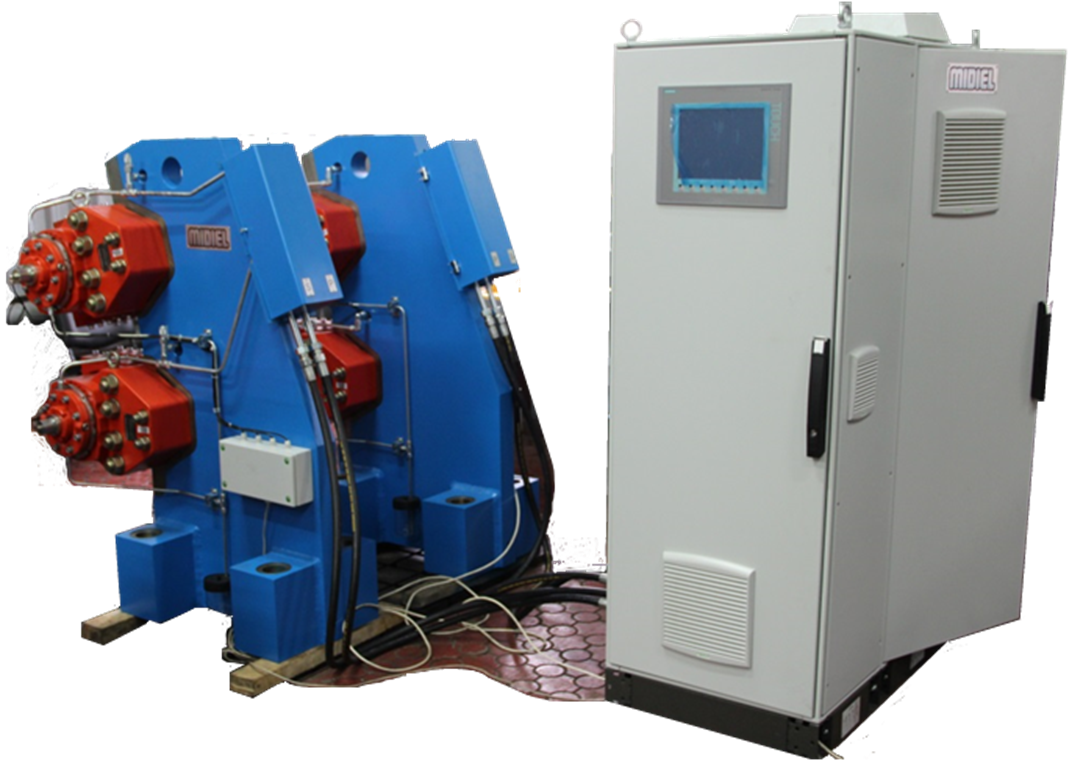
The BSFG 408A and BSFH 515 brake modules are characterized by:
- small air gap, few moving parts, and fast actuation;
- simple design, adjustment and tuning, relatively low price level due to the mass production;
- large friction lining area, low operating temperature of friction lining and brake disc, increased service life of friction lining;
- Normally closed design ensures that the brake responds when the operating pressure drops or disappears;
- drainage system prevents oil from getting on brake discs, high safety;
- the pad position sensors “Disengaged” and “Pad Wear” have an analog output signal;
- friction lining organic, asbestos-free;
- The design of the brake element ensures its operation in humid, dusty and aggressive environment.
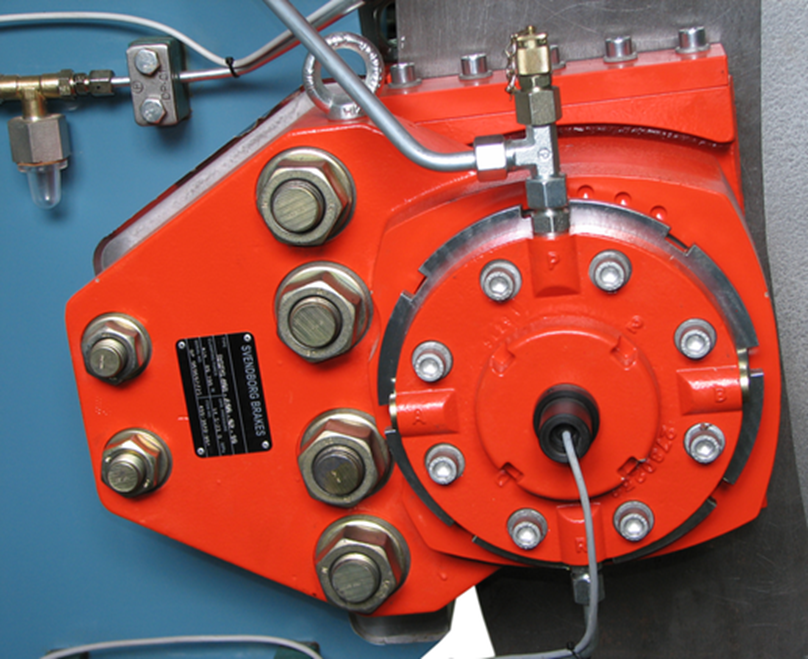
The disc brake consists of two brake circuits, which ensures high reliability of the system as a whole and makes it possible to perform safety braking even in case of a single fault in one of the circuits. The disc brake provides adjustable safety braking under various loads. The actual deceleration is measured by a sensor mounted on the hoist shaft. The microprocessor control system ensures rapid application of braking torque to achieve the required deceleration. Backup power supply provides uninterrupted braking control in case of main power failure. The automatic disc brake control system (ADCS) provides the following modes of safety braking:
- constant torque safety braking – mode, in which the brake modules are set to a constant pressure. As a consequence, there is no adjustment of the braking torque during safety braking. If a fault occurs in one of the circuits, the second circuit corrects the pressure setting, ensuring that the braking torque remains unchanged;
- selective safety braking – mode, in which the pressure in the brake modules is calculated by a given algorithm, depending on the current parameters of the lift machine operation (possible accounting of the direction of movement, position of the lift vessels in the trunk, the load). In this case the pressure regulation is not performed during the safety braking. If a fault occurs in one of the circuits, the second circuit corrects the pressure setting, ensuring that the braking torque remains unchanged;
- safety braking with constant deceleration – the mode under which a constant deceleration is maintained, regardless of the direction of movement, position of the lift vessels in the trunk and the load. Constant (the same) deceleration during safety braking in all operating modes of the lifting machine is provided by regulating the pressure and, as a consequence, the braking torque. The control system generates a feedback signal on speed signals received from two incremental encoders installed on the shaft of the lift machine.
Block diagram of the automatic disc brake control system
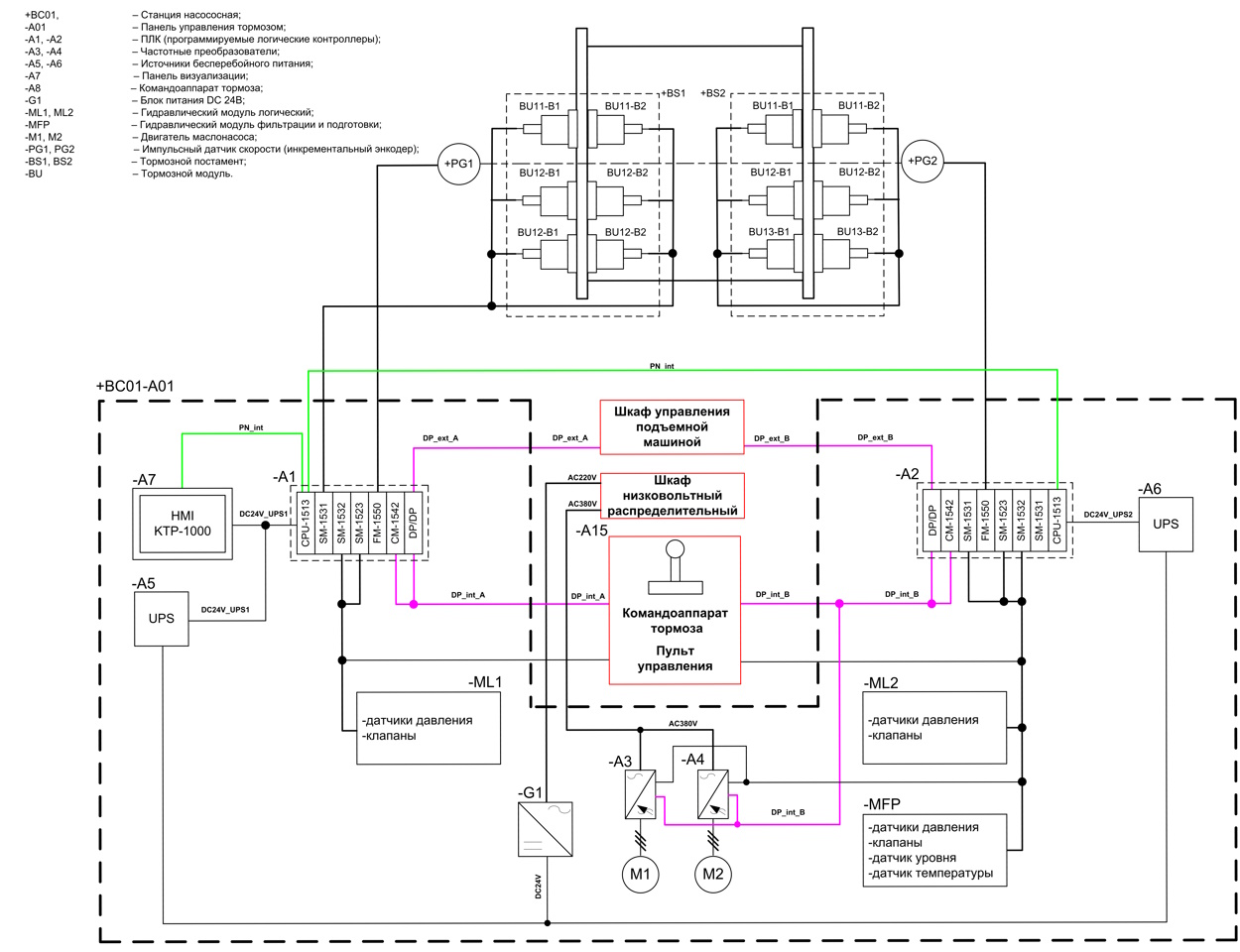
A distinctive feature of the ADCS is the use of modern programmable logic controllers Siemens Simatic S7-1500, and the system uses PLCs based on central processing units (CPU) of various models.
The pumping station has a double-circuit modular design, which makes it possible to divide the system into two independent controlled brake groups. The station circuit modules are fully interchangeable. Independence of the station circuits makes it possible to use it in brake systems of double drum hoisting machines and machines with one split drum.
Design versions of disk brake pumping station
Most of the control devices of the pumping station are seat-type valves, so there is virtually no leakage in the system. In view of this, the oil does not actually warm up, which allowed the use of a tank with a capacity of only 50 liters, which corresponds to the fire safety category B4 (for the entire building category D) and eliminates additional costs for fire-fighting equipment. The station consists of two pump units installed on vibration mounts. The pump supply is frequency controlled from 0 to 30 l/min. The control algorithm provides for switching-off the pump units after the hoisting machine stops and decreasing the pump units’ speed to minimum (only for leakage compensation) after the command “de-releasing” is finished. The high speed of the system is provided, which allows the 2-circuit station to control 40 pairs of BSFG 408 A type modules or 20 pairs of BSFH 515 type modules. Thus the braking system of NPF “MIDIEL” ensures safe operation of the mine hoisting unit within the whole possible range of loads. The pumping station has low power consumption; a heating element is provided in the tank to start the station in the cold time. For heat utilization fans and a low-noise oil-air heat exchanger with an additional filter are installed in the station enclosure. The unified pump station is made on modern element base of world leaders in production of hydraulic drives and devices of electric automatics (HYDAC, SIEMENS, S.A.M.HYDRAULIK, KTR etc.)..
The control program includes continuous diagnostics of the system components, as well as monitoring changes in oil chemistry, dissolved water in oil and oil solids content. This allows the system to respond quickly and unambiguously to any malfunction, as well as promptly notify maintenance personnel of the need for oil changes, since statistics show that 70% of failures in hydraulic drives occur due to poor condition of the working fluid.
As an option, the station allows the “gravity descent” mode – lowering the loaded vessel (raising the empty vessel) under the action of gravity. For this the braking system is additionally equipped with a DC-AC type inverter and a galvanic battery.
After manufacturing, the system is checked and tested at the production site.
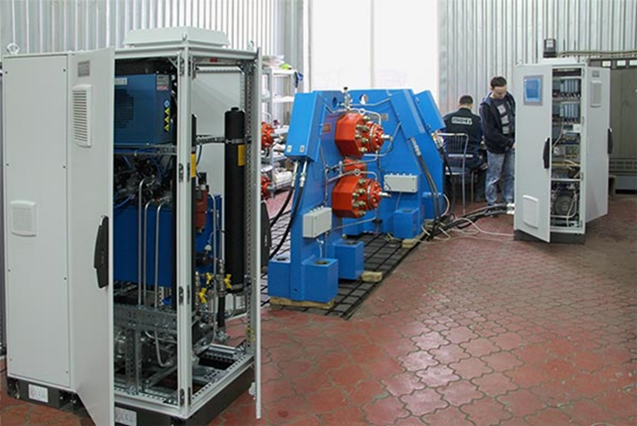

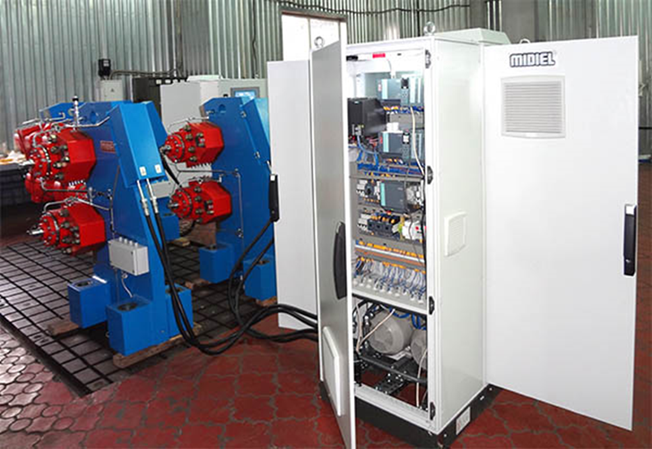