Electric drive
MIDIEL Group completes newly manufactured and modernized mine hoisting machines with modern and energy-efficient electric drive systems. The composition and technical characteristics of the electric drive system of each of the lifting machines are individual and are selected on the basis of the calculations performed, based on the purpose of the machine and its required operating parameters.
For newly developed lifting machines, as a rule, variable AC electric drive systems based on synchronous or asynchronous motors are offered. Depending on the required drive power, the purpose and design of the lifting machine, both a geared drive using high-speed asynchronous electric motors and a gearless drive using low-speed synchronous electric motors are offered. For modernized hoisfting machines, both AC and DC electric drives can be offered.
Overview table of used electric drives
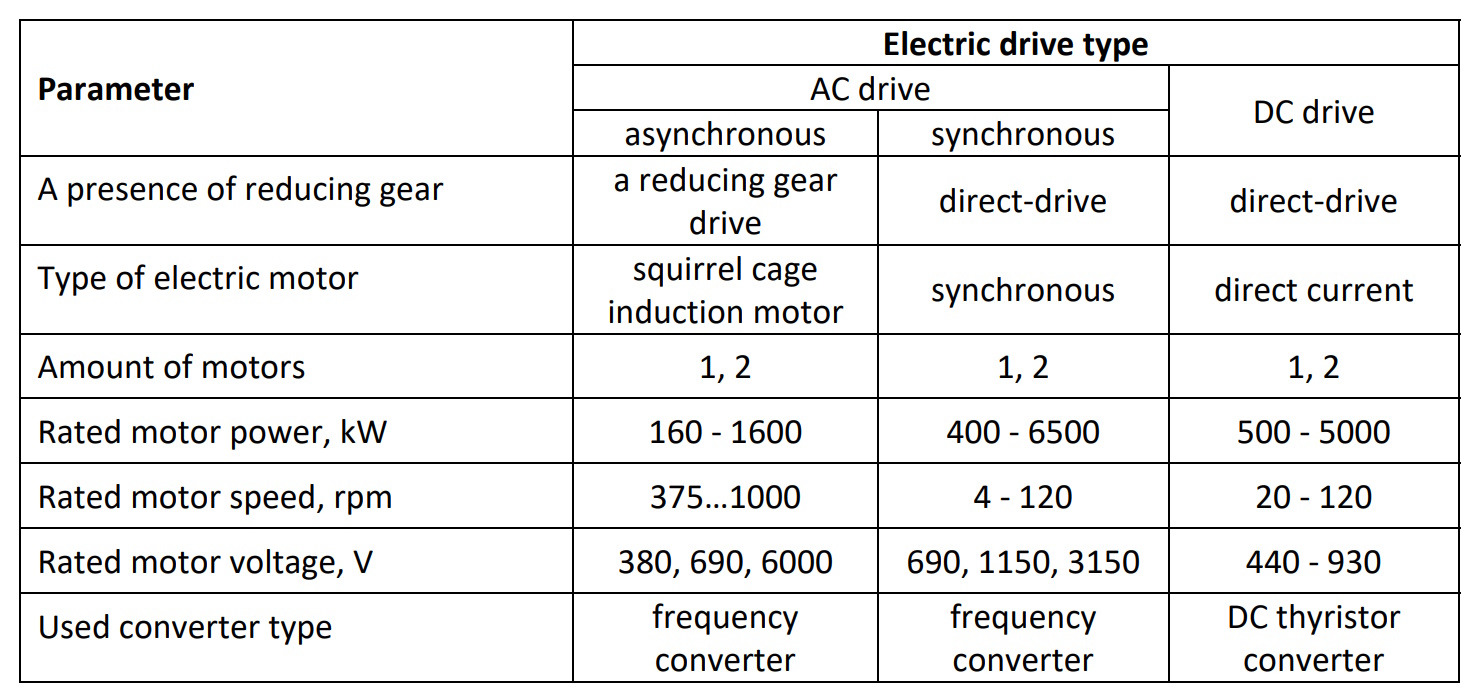
The proposed induction motors with a squirrel-cage rotor synchronous low-speed motors are from leading European companies: Siemens (Germany), ABB (Sweden), Focquet (Belgium), DFME (Poland), etc .
Hoist electric motors
The adjustable electric drive is implemented on the basis of frequency converters, both low-voltage and high-voltage manufactured by leading European companies: Siemens and ABB. All frequency converters used are highly reliable and adapted to the conditions and technology of mine hoisting.
The electric drive system of the hoisting machine provides:
- continuous operation of S9 according to IEC 60034;
- motor speed control;
- starting, accelerating, working at a constant speed, braking, reaching at a reduced speed according to the specified programs of movement in both directions.
In comparison with the previously widely used electric drive systems with a phase rotor or direct current, the proposed drives based on frequency converters have the following advantages:
- high energy efficiency due to the use of frequency converters with energy recovery into the supply network;
- the motor and frequency converter operate with a power factor close to 1 during the entire ascent-descent cycle. At the same time, losses in the electric drive and supply network are reduced;
- voltage drop in the supply network when starting the engine; it is possible to operate electric drives with low-power supply networks;
- low harmonic level. Basically, all harmonics below the 25th are eliminated by the built-in filters by the phase control software. The use of separate filter compensating devices is not required;
- high accuracy of maintaining speed, the ability to obtain any stable intermediate speeds when lifting and lowering cargo, people, equipment;
- high reliability of operation due to the absence of electromechanical switching devices (motor manifold, power contactors, etc.);
- compact design and small dimensions, and consequently, reducing the cost of capital construction;
- Easy maintenance due to advanced diagnostic function.
The required technical parameters of the frequency converter are determined by the Supplier, taking into account the parameters of the received engine during the technical design. The low-voltage frequency converters of the SINAMICS S150 series manufactured by Siemens and ACS880 manufactured by ABB are the world leaders in sales among low-voltage converters due to a number of impressive advantages:
- low operating costs;
- precise process control;
- low maintenance cost;
- increased productivity;
- high reliability;
- Intuitive interface.
These converters include an active power supply module that provides energy transfer to the intermediate circuit (DC link) and energy recovery when the engine is operating in generator mode, and an engine module that provides four-quadrant engine control. The active power supply module provides an adjustable DC voltage that remains unchanged when the supply voltage changes within the permitted tolerances, in addition, active network modules consume almost sinusoidal current from the network, and practically do not adversely affect the supply network.
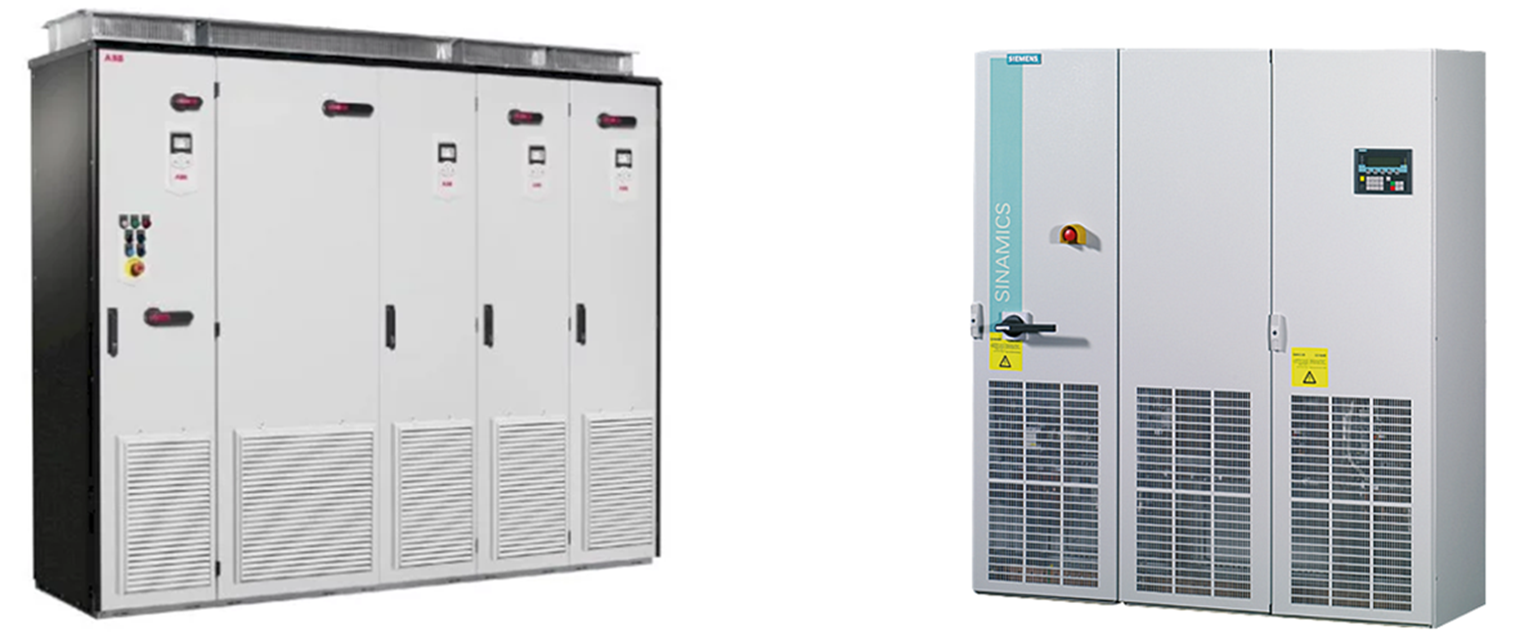
- exceeding the ambient temperature;
- excess voltage on the DC bus;
- reduced voltage on the DC bus;
- overheating of the converter;
- lack of supply voltage phase;
- overcurrent;
- exceeding the permissible power;
- short circuit.
As a rule, the electric drive is controlled using the widely used Profnet and Profibus communication buses. Low-voltage electric drives are equipped with dry-type converter transformers with cast insulation for coordination with the Customer’s power supply network. At the request of the Customer, power cable products can be supplied with an electric drive in an amount sufficient to connect the converter to the motor and converter transformer. Additionally, the electric drive can be equipped with a 6 (10) kV high-voltage switchgear according to a questionnaire agreed with the Customer.
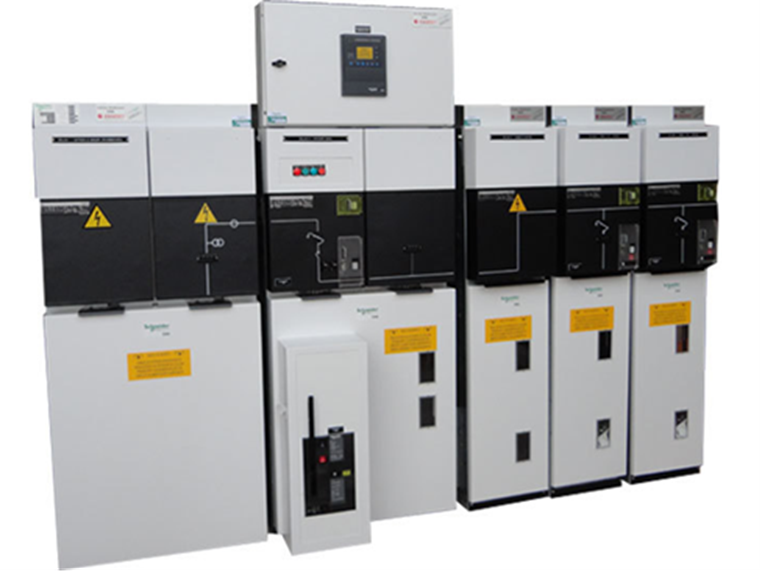